The solution for custom designs on t-shirts, hoodies, bags, sportswear and workwear: DTF Digital Transfers.
Thanks to the combination of digital printing and heat transfer technology, textile transfers can be printed in small quantities, full-color and in the shortest possible time. Thus, the outstanding opacity and feel known from plastisol and screen printed transfers is now also available in small quantities.
DTF digitally printed transfers such as our DHT Tex are produced using the so-called DTF (Direct To Foil) printing process. In this printing process, the printed image is printed digitally, which makes it possible to implement multicolor designs, gradients and small batch sizes in particular.
Only high-quality materials and printing machines are used for our DTF transfers:
✔ Inks with OEKO-TEX certification
✔ Printer with specially created color profile
✔ Hotmelt adhesive with low activation temperature
✔ Carrier film for cold or hot peel
In addition, we offer maximum support for data creation and optimization with our in-house prepress. And after 5 days at the latest, the transfers are on their way to you.
Choose between transfers for light or dark textiles as well as special effects like the "Athletic Print" for sportswear, which improves the breathability of the print.
Print results are:
✔ Safely washable at 40°C.
✔ Strongly stretchable
✔ Pleasant to wear
✔ Color intensive, even after frequent washing
Contact us
And be amazed by the quality of DHT Tex transfers
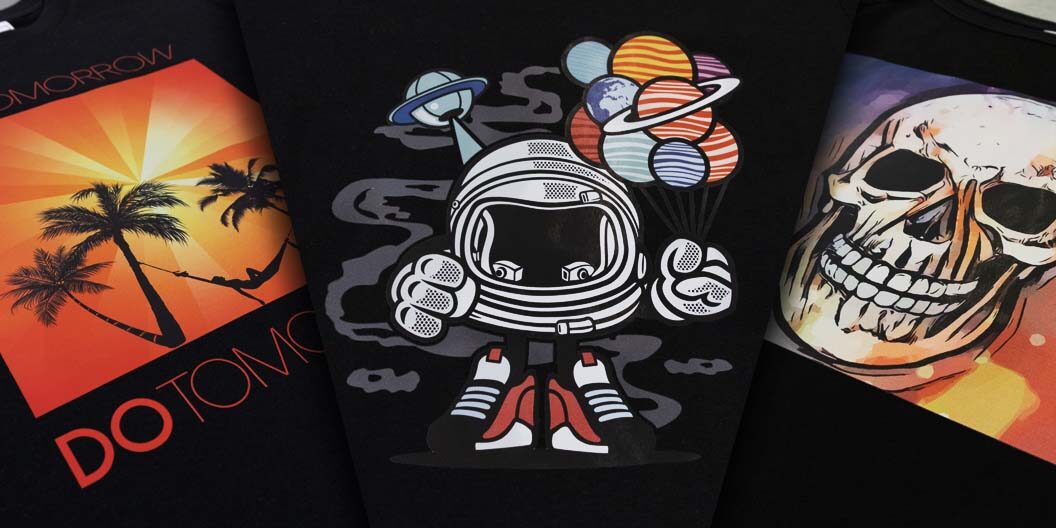
Production of DTF transfers
In this digital printing process, two or four print heads are usually used to print the four process colors and white onto the carrier film. The colors are applied first and then the white. To prevent the water-based inks from running, a special film with high in uptake is used combined with a heated printing area. In this way, the inks are absorbed and dried to such an extent that overprinting is possible without the inks running.
After all the inks have been printed, the still moist print image is sprinkled with the hot-melt powder and the excess is tapped off. This method guarantees that adhesive is only applied to the ink and not to the film.
Finally, the DTF digital print transfer is dried and can either be shipped as a roll or cut into the desired formats.
DTF Printer for Digital Transfers
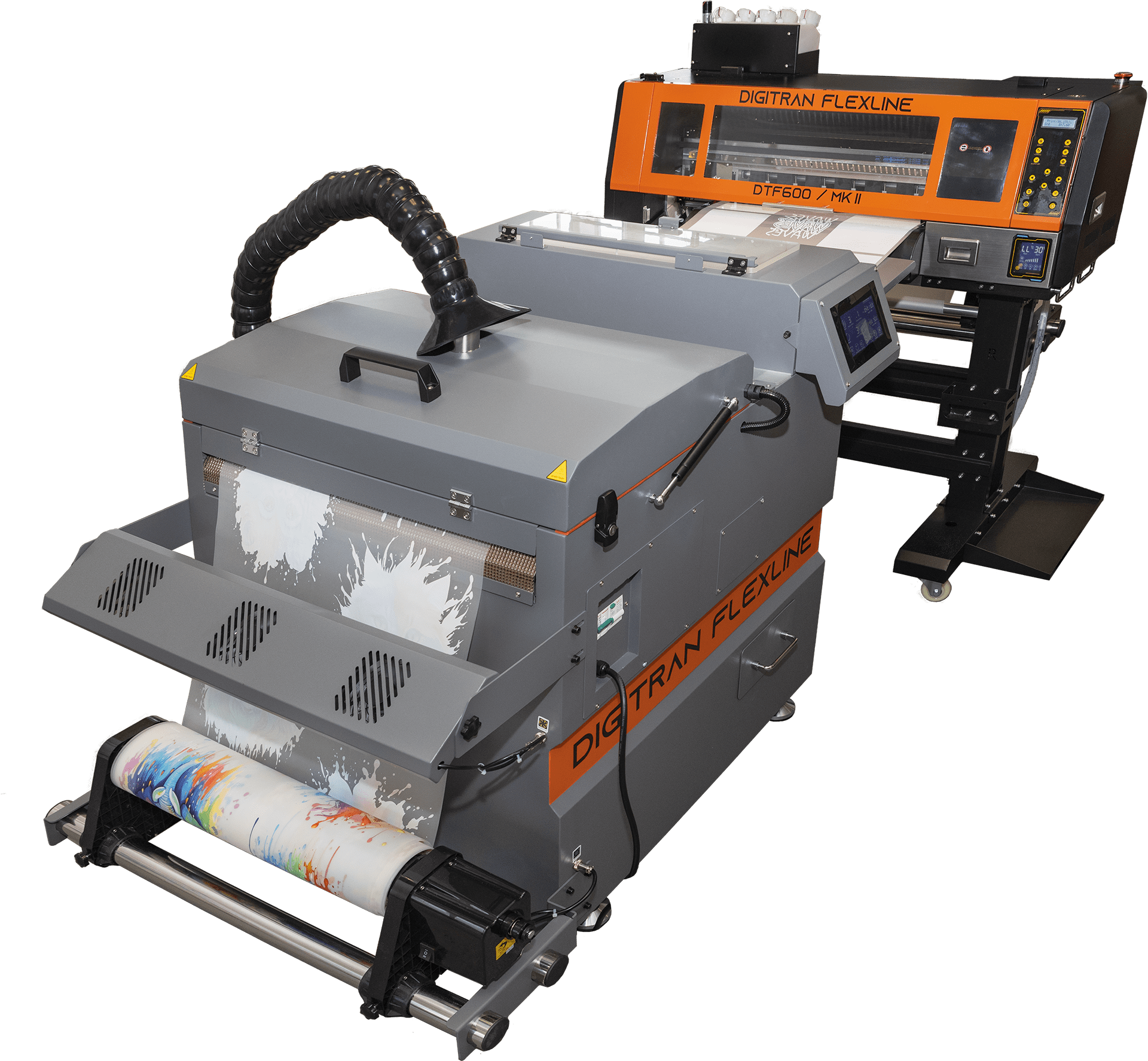
To be able to produce transfers using digital printing technology yourself, a DTF (Direct to Foil) printer is the best choice. Such machines consist of a printing unit and a finishing unit, which are built in line. Such a machine system is the DIGITRAN FlexLine DTF600 MK-II.
This DTF printing machine is equipped with two high-quality and durable print heads and optimized for FlexInk inks. High ink coverage, color fastness, washability and OEKO-Tex certification are just a few of the advantages this system offers you.
In addition, this system relies on a hot-melt powder with which cotton, polyester as well as blends are easy to print. A brush also ensures that the powder is evenly applied to the print without clumping. After shaking off the excess, the printed image is dried by 3 IR emitters. Finally, the printed film is then cooled down and wound onto a roll.
Thanks to this fully automatic printing technique, full-color transfers can be printed quickly, easily and cost-effectively. Without screen production, cleaning or additional drying.
Click the button to contact us directly and receive personal advice. So that your products can also benefit from this unique, clean and digital printing technology as quickly as possible.
Further Posts
What is DTF? We explain it!
Welcome to the fascinating world of DTF printing, where flexibility and quality come together. Dive into our detailed insight into the process – from the innovative DTF printers to the automatic powder shakers to the transfer press. Discover how this technology is redefining the boundaries of printing.
Besides many other factors that can influence the heat transfer process, the three most important ones are heat, time, and pressure. No matter if it is a textile transfer or a transfer for packaging applications, you should know about the effect of these parameters and how a transfer is affected by them.
Textile heat transfers come in three technologies when it comes to peeling. This can be “hot peel”, “cold peel” or “hot split”. But what is the difference between them?
Heat transfer decorating at up to 600 textiles per hour – with a single operator!
This is what the TURBOTRAN 6.1 is build for. The fastest, fully automatic heat transfer machine in the textile industry.
Posts from other topics
Today we’ll start our new “Color Makes The Difference” project! Every week we will post a product printed using our digital heat transfer decals to keep you inspired! For this one we picked a PP (polypropylene) mascara bottle which was
Ever wondered if there is a smaller quantity, high quality alternative to conventionally printed heat transfers? The answer is YES! DIGITRAN heat transfer decals are digitally printed and fill in this gap! DIGITRAN digital heat transfers are designed for cosmetic
- « Previous
- 1
- …
- 3
- 4
- 5