Are you having problems when printing on polypropylene (PP)? Not with DIGITRAN heat transfer images. Our digitally printed transfers can be applied even on untreated PP!
Polypropylene (PP) is a material used in many applications from cosmetics to promotional products due to its properties such as hardness, resistance and costs. However, what are important and desired properties for some are an issue for others. That's because PP is not so easy to print on. Here you can find out why this is so and what is needed to print products made of PP, without any pre-treatment.
Polypropylene (PP) is a plastic that belongs to the group of polyolefins. In addition to polypropylene, polyethylene (PE) and PTFE (also known as Teflon) are representatives of this group. These plastics are known from plastic bottles, cream tubes, mascaras or as the coating on a frying pan. Despite these different applications, these plastics and their variations have one thing in common, a very low surface tension. And this is where the difficulty begins.
Put simply, surface tension indicates how well a surface can be wetted by something. Water, with a value of approx. 72 mN/m or dyn/cm, has a very high surface tension. Polypropylene (PP), on the other hand, has a dyn value of approx. 30 and thus a very low surface tension. The front-runner, however, is PTFE with approx. 18 dyn/cm, which is also the reason why nothing really sticks in a frying pan. The crux is that the to be printed material should have a surface tension that is about 10 dyn/cm higher than the surface tension of the ink, varnish or adhesive applied.
This results in the challenge you face when printing polypropylene (PP). More specific, it lies in the fact that the surface tension makes proper wetting difficult or impossible. Nevertheless, we see printed products made of PP, so the problem has been solved, right?
Pretreating Polypropylene (PP)
One way to solving the surface tension problem is to pretreat the plastic. This means that the surface of the PP is changed prior to printing to achieve a better wetting behavior. A number of methods are available to achieve this. These processes include technologies that oxidize the product's surface and form polar groups there. The three common technologies are a flame, corona or plasma pretreatment.
In these processes, the product is either moved pass an open flame, "irradiated" with a generated plasma or by a high-energy corona discharge.
As an alternative to these process solutions, there are other options in the form of primers. These systems are liquids with very low surface tension or aggressive chemicals. In particular, the solvents isopropanol, also known as IPA, ethanol and n-heptane are used because of their low surface tension and short flash-off times to apply a thin coating film with higher surface tension. In this way, the surface of the PP is replaced by a very thin varnish of another material, which allows better adhesion.
Both ways lead to better adhesion, but this optimization is not free.
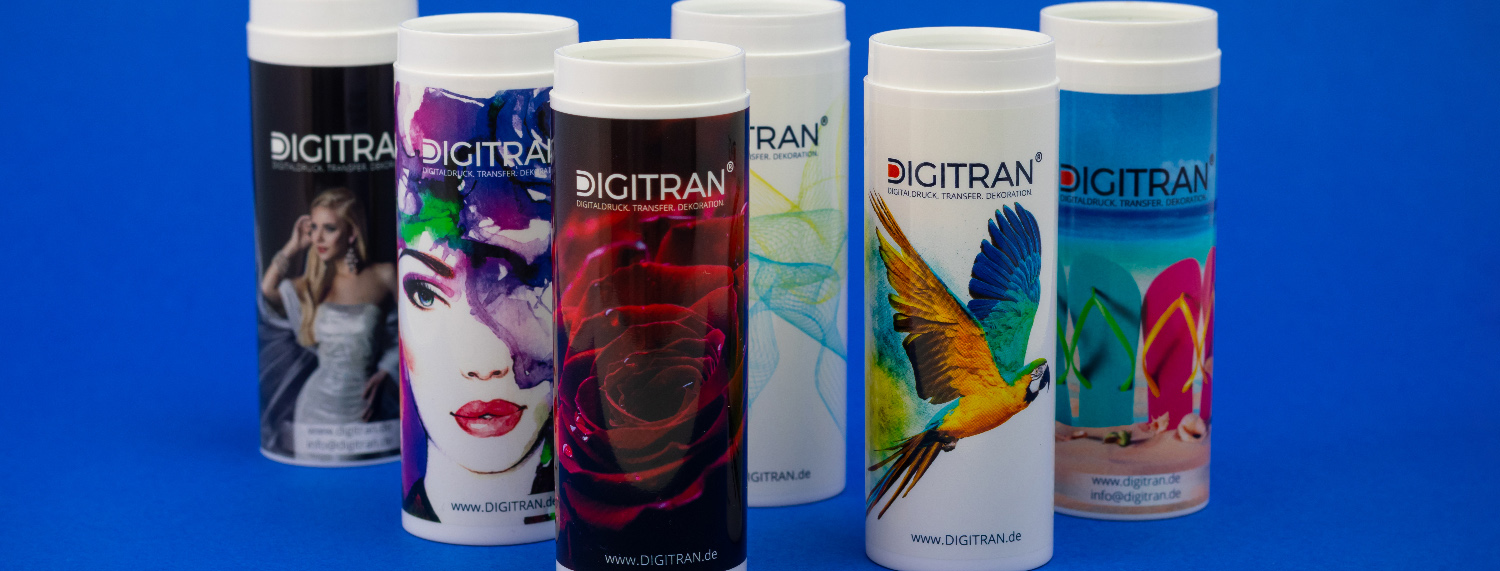
Additional costs that can be saved
All types of pretreatment have one thing in common, they are an extra step in the process and cause additional costs. In the case of a pretreatment with flame, corona or plasma, the equipment alone can quickly cost several tens of thousands of euros. In addition, electricity, gas and compressed air are constantly consumed. Furthermore, in case an external or offline solution is used, the time required for handling must be taken into account as well.
When using primers on PP, the situation is not much better. Although no expensive equipment is required for priming, the primers themselves are an expensive product. Likewise, the common application method of soaking a rag and rubbing the surface with it is labor intensive. In addition, the chemicals used are not safe, which is why the worker should wear appropriate protective equipment. Last, the primer must flash off or dry, producing solvent vapors.
Regardless of which way one goes, it is not a good solution but a compelling evil. However, this evil does not have to be.
Printing polypropylene, without pretreatment
The good news is, there are solutions for printing on polypropylene (PP) that work without any pretreatment at all. Furthermore, these can be without VOCs, UV-curing or expensive equipment. This solution is the heat transfer process. More specifically, digitally printed heat transfers from DIGITRAN.
One of the DIGITRAN products are digital heat transfers for untreated PP. These are characterized by the fact that they can be applied to polypropylene without any pretreatment. All that is needed are the transfers and a heat transfer machine.
During the decoration process, a hot transfer roller presses the transfer onto the product. The heat activates the image and makes it bond with the product. After that, the carrier material will be peeled off and the printing process is complete. Neither flash-off, drying nor curing is necessary. In addition, the prints are odorless and can be used without any protective equipment or other special requirements.
This means that cosmetics, promotional and industrial products can be printed quick and easy - even if they are made of PP. At the same time, the digital printing technology offers a resolution of 1200 dpi as well as the production for small and large print runs.
Click this button to get in touch with us for a personal consultation. To make sure that your products can benefit from this unique, clean and digital printing technology as soon as possible.
Further Posts
CMTD – 6 feet of fine art. High-quality digital printing for folding meter sticks – without smudges.
Printing on each segment’s edge and not in-between them is the printing challenge of folding meter sticks. And with heat transfers you can achieve just that.
Folding meter sticks printed with digital heat transfers benefit from a high resolution digital print. Not only giving a great price for small quantity multi-color prints, but also being very durable.
Would you think that 1200dpi and 1200dpi digital printing is the same? You probably would.
But actually no, not even close!
Especially when it comes to photo-realistic printing and skin tones the print quality must be on point. The confusing part is that even though both prints shown in the photo have a resolution of 1200 dpi, they are obviously not the same. But how does that come?
Why cosmetic tubes are perfect promotional products? Because they are compact, useful and give enough space for your message.
And we are here to get them printed, also in small quantities!
As a contract decorator who prints your tubes just in time and in almost any quantity, or as your partner for heat transfer machines as well as digital heat transfer decals, we have the perfect solution for you.
What you should know about the advantages of printing different names, languages, numbers and codes – in one run!
Starting with printing different names on promotional products over serialized special editions to a print run with every image being different. With digital heat transfers you can achieve all this. Without UV, without solvents and without stopping your heat transfer machine.
3 sides, 3 different photo-realistic images.
That is what a paper cube box can look like when you print it with DIGITRAN digital heat transfer technology.