The unveiling of DTF printing technology: the printing process from print to transfer.
Today it's a detailed exploration of the fascinating world of DTF printing - a process that combines transfer and digital printing to achieve outstanding print results. Let's go through the seamless flow of this process step by step, starting with the key component, the DTF printer.
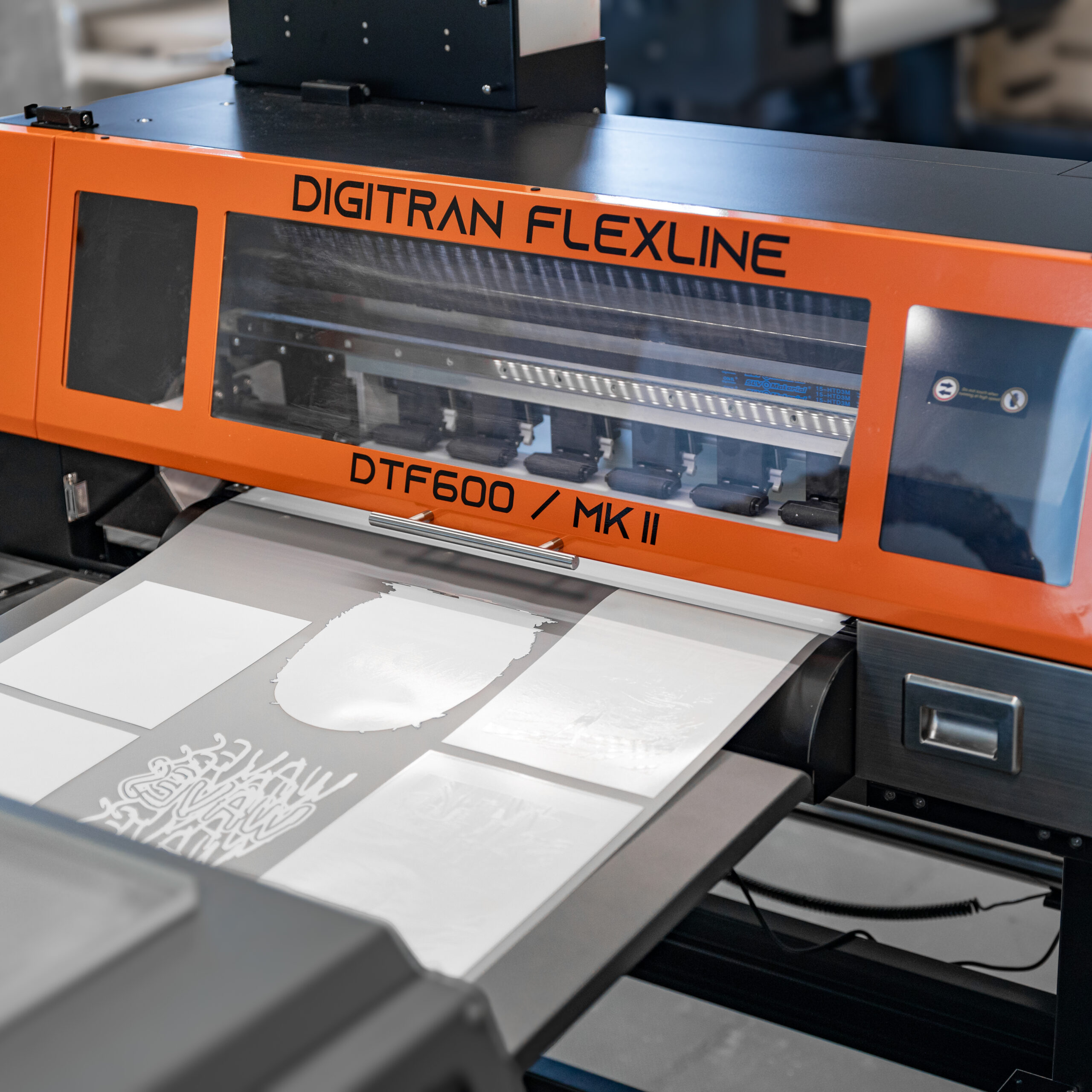
Step 1: The DTF printer - printing without screens and co.
The DTF printer forms the starting point of this process and acts as the main hub for the production of designs. With water-based pigment inks in CMYK+white, it enables a wide range of printing options. Everything from logos and company names to photographic images can be printed in any quantity. The particular challenge lies in handling the highly pigmented white ink, for which our printers are equipped with an stirrer and a circulation pump and filters. Automatic cleaning cycles and regular maintenance ensure that the opacity is perfect and the print head does not clog.
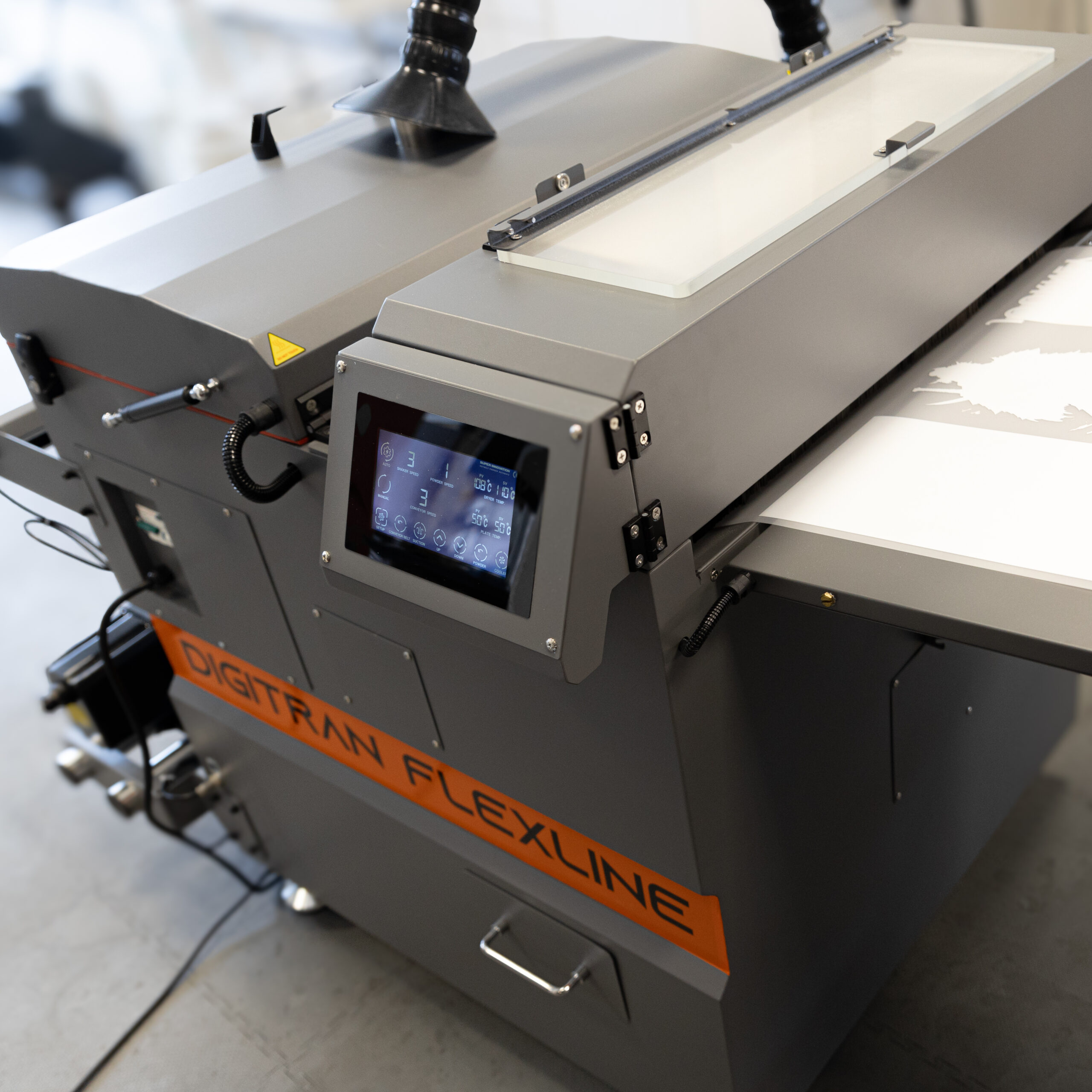
Step 2: Automatic powder shaker - Preparing precise adhesion
After printing comes another crucial step in the process - the automatic powder shaker. This device ensures an even distribution of hot-melt adhesive powder onto the printed film. The flexible adhesive powder acts as a bonding agent between the textile and the ink so that the transfer can be fixed to the textile surface. Furthermore, excess adhesive is tapped off and the printed image is dried. To remove excess moisture before powdering, the line begins with a preheating plate. A compact extraction unit above the drying channel filters the vapors directly at the machine and keeps the air clean.
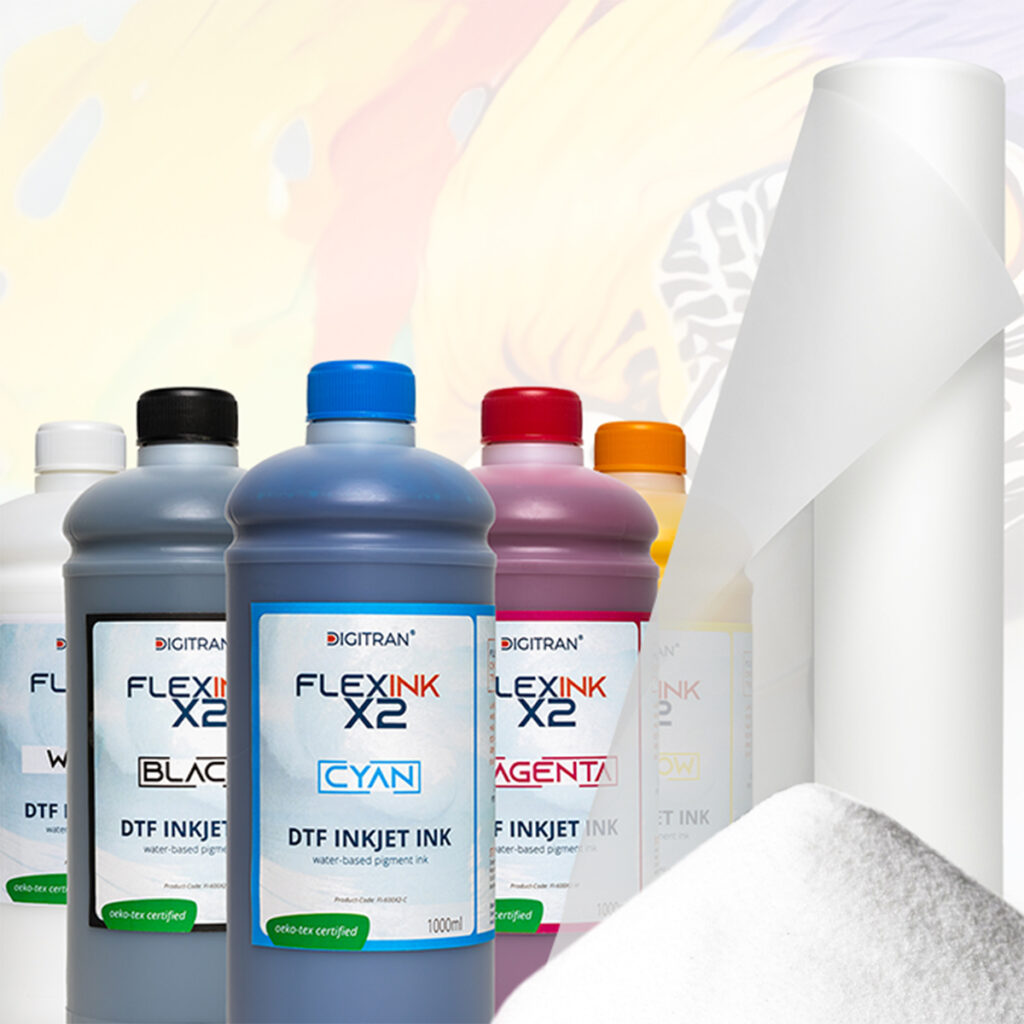
Step 3: Consumables - the basics of the masterpiece
The consumables play another key role. In addition to their individual properties, they must be perfectly matched to each other. The release film should absorb the ink, create an appealing surface and, ideally, be thermally stabilized and anti-statically treated. In addition, the variants range from cold to instant peel, which differ in terms of when and how they can be peeled off. In addition to being wash-resistant, the ink must achieve a high level of coverage with minimal amount of ink and must not tear after application. Finally, the adhesive powder is responsible for adhesion and durability, with grain size, melting temperature and hardness being a few key properties.
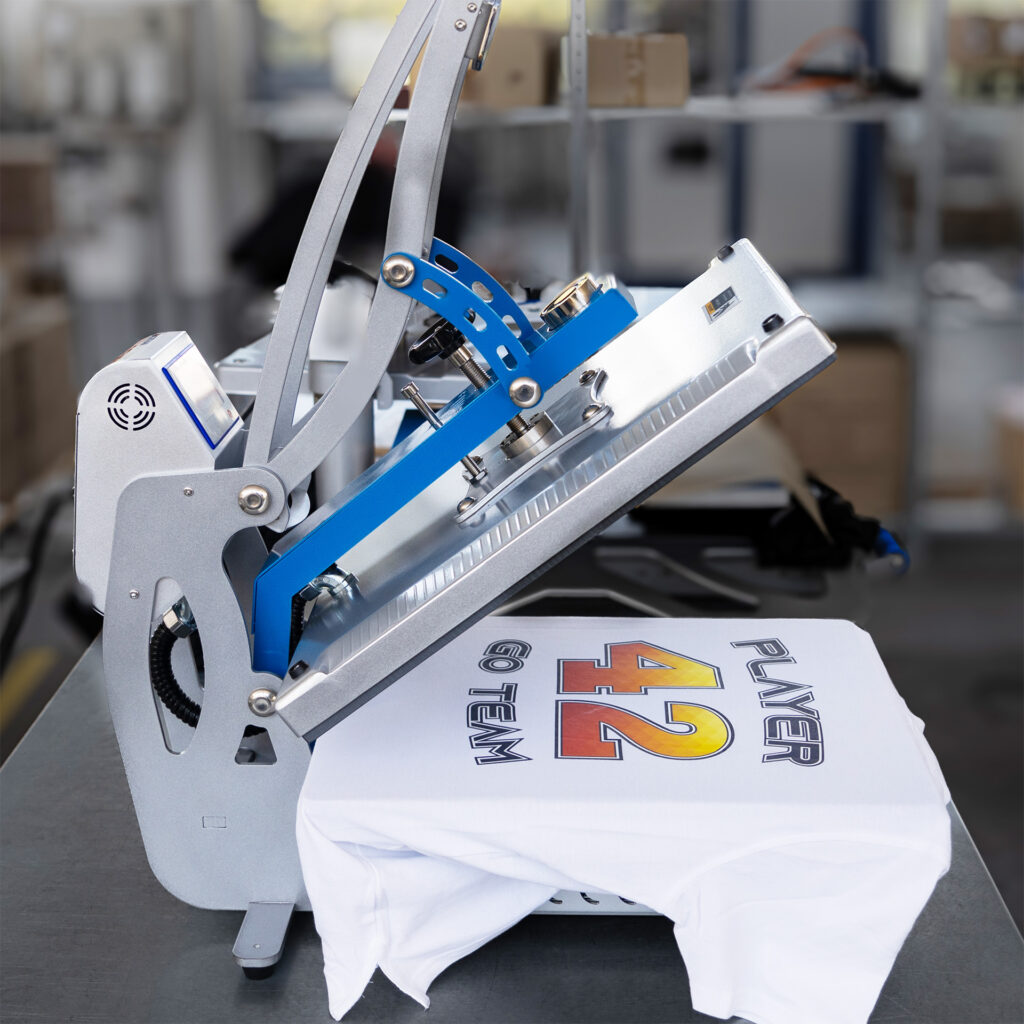
Step 4: Transfer press - The last piece of the puzzle
Once everything has been printed, powdered and dried, it's time to apply the transfers. For this, a heat transfer press is needed. It doesn't matter whether you have a simple, mechanical press or an ultra-modern, fully automatic transfer machine. The main thing is that the temperature and contact pressure are balanced and adjusted to suit the textile. The combination of heat, pressure and time melts the adhesive and the printed image bonds with the textile. Fast transfers are ready after just 7 seconds. Once the transfer is complete, all you have to do is peel off the backing film and you're done.
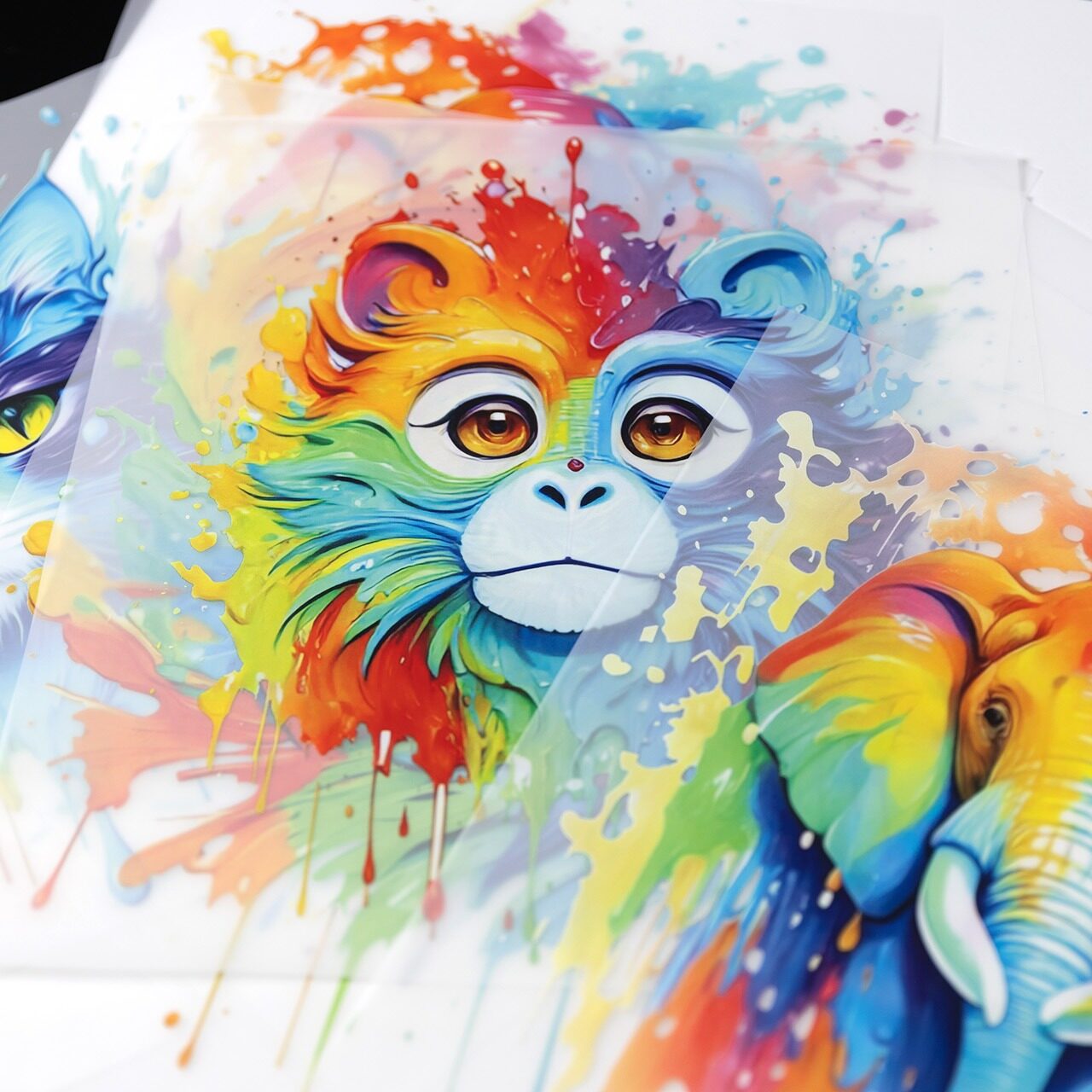
Step 5: The application - The holy trinity
Once everything from the print data to the dried image is perfect, all that remains is to apply the transfer. There are three key points to consider here. Pressure, time and temperature. These values depend on the transfer, transfer press and textile. A separate article on this topic can be found here "HEAT, TIME AND PRESSURE - THE HOLY TRINITY OF HEAT TRANSFER DECORATION". But don't worry, if no information was given during the transfer, 130°C and 9 seconds is always a good start for DTF transfers. In general, if the adhesion is not good, it is better to press a little longer or hotter.
We hope that we have been able to shed some light on the question of "What is DTF printing". Should you have any further interest in this process, our team is available for a personal discussion.
Why get started with DIGITRAN? Because quality and experience go hand in hand.
In an era where DTF printing technology is redefining the textile industry, we are ready to spearhead the way to help you realize the full potential of this technology. We have been at the forefront of DTF since 2019. Both as a printing company and as a partner for machines and consumables. With this mix, we know all the components and peculiarities of DTF printing, so you don't have to gain this experience yourself.
We will accompany you on this exciting journey, where every print is an impressive work of art. We implement your ideas to suit your requirements - let's redefine the printing era together!
Contact Us
for a non-binding and personal consultation on the subject of digital transfer printing.
DTF printers - digital transfers for textiles
Our solution for advanced users.
To be able to produce transfers in digital printing yourself, a DTF (Direct to Foil) printer is the best choice. Such machines consist of a printing unit and a finishing unit, which are built in line. Such a machine system is e.g. the DIGITRAN FlexLine DTF600 MK-II.
This DTF printing machine is equipped with two high-quality and durable print heads and optimized for FlexInk inks. High ink coverage, color fastness, washability and OEKO-Tex certification are just a few of the advantages this system offers you.
In addition, this system relies on a hot-melt powder with which cotton, polyester as well as blended fabrics are easy to print. The powder unit also ensures that the powder is applied evenly to the print without clumping. After tapping, the printed image is dried in a drying tunnel using IR lamps. The printed film is then cooled and wound onto a roll.
Thanks to this fully automatic printing technique, multicolored motifs can be printed quickly, easily and cost-effectively. Without screen production, cleaning or additional drying.
Click on the button to get in touch with us directly and receive personal advice. So that your products can also benefit from this unique, clean and digital printing technology as quickly as possible.
Further Posts
The solution for custom designs on t-shirts, hoodies, bags, sportswear and workwear: DTF Digital Transfers.
Thanks to the combination of digital printing and heat transfer technology, textile transfers can be printed in small quantities, full-color and in the shortest possible time. Thus, the outstanding opacity and feel known from plastisol and screen printed transfers is now also available in small quantities.
Besides many other factors that can influence the heat transfer process, the three most important ones are heat, time, and pressure. No matter if it is a textile transfer or a transfer for packaging applications, you should know about the effect of these parameters and how a transfer is affected by them.
Textile heat transfers come in three technologies when it comes to peeling. This can be “hot peel”, “cold peel” or “hot split”. But what is the difference between them?
Heat transfer decorating at up to 600 textiles per hour – with a single operator!
This is what the TURBOTRAN 6.1 is build for. The fastest, fully automatic heat transfer machine in the textile industry.